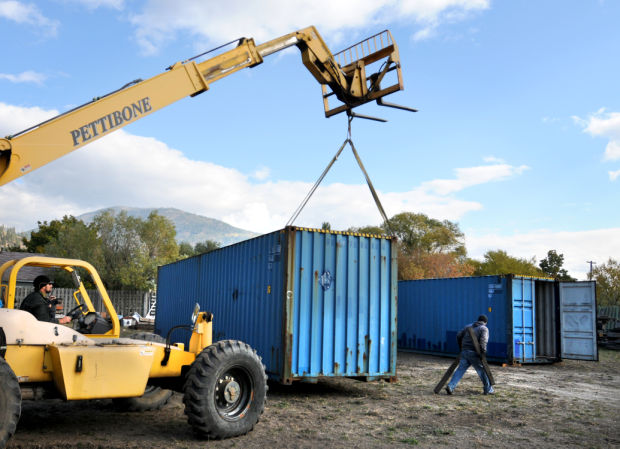
Liquid Planet in Missoula will soon have a new drive-through coffee kiosk made from these two 9,000-pound shipping containers. Pfiffner Design Build in Bonner positions the containers Thursday afternoon at its shop and will soon have the 320-square-foot containers ready for business.
As work began this month at the site of what will become Liquid Planet Montana’s newest location, company owner Chad Morgan awaited the delivery of a 40-foot steel shipping container salvaged from a shipyard in Seattle. The container, after it’s paired with another 40-foot container, will make up the exterior of the Liquid Planet coffee stand, located just outside the entrance to the Missoula International Airport.
The location will include two drivethrough windows and a third for pedestrians.
Missoula-based Liquid Planet has worked hard, Morgan said, to build a name for itself with its lines of all-natural, organic and sustainable brands of beverages, mugs, coffee and tea products.
Now, Morgan wants to build on that mission while introducing Missoulians to shipping container construction.
“It’s a concept that has been used in lots of other states,” Morgan said. “Even Starbucks has made stores out of shipping containers ... You can stack them any which way you want, you can cut out what you want. It’s efficient and quick, and it’s very, very unique in design.”
The containers are affordable, durable, easy to transport and recycled – all of which creates a sustainable building technique that aligns directly with Liquid Planet’s mission.
“We always work to be as green as we can,” Morgan said.
Morgan knew he wanted to build with containers. Earlier this year he came across a new Missoula business that has big plans to use shipping containers as the base for its buildings.
Mont’ainer, founded by Thom Finch and Patrick Collins, orders containers and then designs shipping container buildings for its customers.
Mont’ainer sold the containers to Morgan. Morgan has hired Pfiffner Design Build LLC to turn the containers into the new Liquid Planet location. A self-described entrepreneur, Collins saw the shipping container construction as an untapped business opportunity.
“This isn’t a new concept, it’s been proven,” he said. “It’s not being utilized at as high of a level in the U.S. as it is in other countries.”
Collins said shipping containers have been used around the world to build everything from multifamily housing units to museums and dorms. The University of Amsterdam created the world’s largest shipping container village with its Keetwonen dorms, made of five layers of stacked of shipping containers.
“They can take that and move it,” Collins said.
Most shipping containers come to America full of products on freight ships from China. It isn’t cost-effective to ship containers back, so they’re discarded, Collins said.
Containers cost roughly $3,000 to $5,000 each. According to Collins, the cost to build a multifamily housing unit using shipping containers would run around $80 to $90 per square foot.
Traditional construction costs run roughly $100 per square foot, he said. The real savings, Collins said, comes in the efficient, simple building process. The main structure of the buildings, made of the sturdy steel of the containers, is already complete. Also, the site work and manufacturing work can be done simultaneously, Collins said.
Both Morgan and Collins noted that containers can be transformed easily to create the desired effect.
The shipping containers used at new Liquid Planet location won’t be heavily disguised.
“We’re designing them purposely to look like shipping containers,” Morgan said. “Then we’ll use other recycled materials outside to dress it up.”
Morgan hopes the new location will be open by mid to late November. Mont’ainer has already received a handful of other orders for containers and is having multiple conversations with entities in Missoula about how container construction can be used here.
Collins’ next goal is to create a large scale manufacturing facility where custom homes, multifamily housing units and other container buildings can be made in after they’re ordered online.
“The biggest piece is proving there is a solid demand for this. We’ve pretty well done that,” Collins said. Morgan hopes Liquid Planet can expand on the shipping container concept as well.
The goal is to use shipping containers as the base material to create easily reproducible blueprints for future stores and kiosks.
“From our end, this is the first test location. We’re going to use that as the model to produce future models we can build in Missoula and then ship anywhere in the country as we grow and franchise,” Morgan said.
Manufacturing work on new Liquid Planet’s building is being done at Pfiffner’s site in East Missoula. Finishing work will be done on site. Liquid Planet is close to finishing its reproducible franchise concept, Morgan said. Building options will include “starship” stores, which are full stores that include a retail space, beverage bar, kitchen and seating areas. Smaller “moonshops” have limited seating and retail space. “Satellites” are smaller drive-up spaces similar to the new location being built in Missoula.
If all goes as planned, all the stores will be manufactured in Missoula using shipping containers and as much local material as possible, Morgan said.
“We have the ability to adapt the designs to any kind of environment. Our goal is to not be cookie-cutter,” Morgan said. “Our goal is to have a cool concept that’s duplicatable but also customizable.”
No comments:
Post a Comment